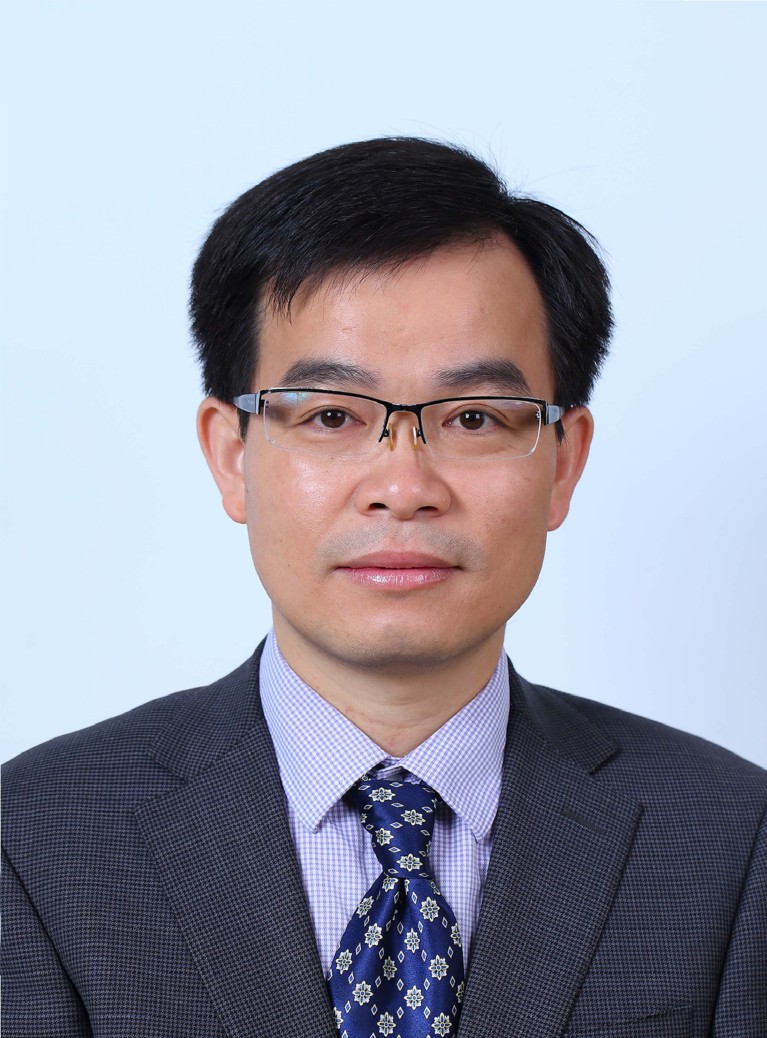
Fei Tao, Vice Dean of the Institute of Science and Technology, Beihang UniversityCredit: Beihang University
Digital twins, comprising five dimensions including physical entities, virtual models, data, services, and connections, can be used to improve aspects of production, operations and business processes. Here, Fei Tao, discusses the Digital Twin Project, a collaboration between Beihang University and the First Research Institute of China Aerospace Science and Technology Corporation.
Can you tell us a little about the digital twin research field?
Digital twin is an interdisciplinary research field which includes engineering, computer science, automation and control, and so on. But due to the multidisciplinary nature of the field, it also touches on materials science, communication, operations management, robotics, medicine and other disciplines. A keyword analysis indicates that digital twin, ‘smart manufacturing’, ‘big data’, ‘cyber-physical system’, and ‘digital economy’ are closely related fields.
Digital twin publications have been produced by researchers from more than 80 countries. And according to a literature review conducted using Scopus, the field started a period of rapid growth around 2016, with the number of digital twin publications doubling every year thereafter. Due to its wide range of applications, we expect that digital twins will attract more scholars to conduct more in-depth research in the future.
How can digital twins be used by industry?
Based on more refined and dynamic models as well as richer data drives, digital twins have played an important role in operation monitoring, simulation, optimization, predictive maintenance, and supply chain optimization. Take the digital twin shop-floor, proposed in 2016 by our group, as a specific example. It can improve the efficiency of operation, control, and management by achieving a deep understanding, correct reasoning and precise operation of objects in the physical space and digital space of a shop-floor.
Now, more and more companies are using digital twins to improve their efficiency–Siemens, ANSYS, Dassault, Airbus, Lockheed Martin, and GE, for example. And according to a survey published by Gartner in 2019, 75% of organizations involved in IoT projects were either already using digital twins or planning to within a year.
The future development prospects of digital twins are broad. They have been applied to 15 fields including aerospace, smart manufacturing, smart cities, construction, medical, robotics, ships, automobiles, rail transit, industrial engineering, agriculture, mining, energy, and the environment. Indeed, a report released by MarketsandMarkets predicts that by 2026, the digital twin market will reach US$ 48.2 billion.
What are the scientific challenges of digital twins?
The Beihang Digital Twin Research Group proposed a digital twin five-dimensional model in 2018, the dimensions being: physical entities, virtual models, data, connection and interaction, and service/ application. At present, the digital twin five-dimensional model has been applied in ten fields including manufacturing, satellites, automobiles, ships, aircraft, smart cities, etc. by ten group enterprises.
The most notable challenges in the physical entities dimension include realizing the intelligent perception and interconnection of multi-source heterogeneous physical entities; and obtaining multi-dimensional data of physical entities in real time.
Challenges in the virtual model dimension include building a dynamic multi-dimensional, multi-space-time scale high- fidelity model; ensuring and verifying the consistency, validity, and reliability of the model; and realizing the assembly and integration of a multi-source, multi-discipline and multi- dimensional model.
Realizing both the real-time collection and efficient transmission of multi-source heterogeneous data and the deep integration and comprehensive processing of cyber-physical data are the main problems in the data dimension. Whereas cross-protocol/cross-interface/cross-platform real-time interactions and realizing the iterative interaction and dynamic evolution of data-model-application are challenges being investigated in the connection and interaction dimension.
The most challenging problems in the service/ application dimension are providing services that meet the needs of different fields, different levels of users, and different business applications based on multi-dimensional models and data, and realizing the value-added efficiency of the on-demand use of services.
For those interested in the practical bottlenecks in the field, in a comment published in Nature in 2019 we discussed how to facilitate the collaboration of experts in different fields and disciplines, and how to combine industry, universities, and researchers to encourage innovation.
How can digital twin research and applications be promoted?
Mostly through dedicated journals and international conferences. In 2017, myself and scholars from 12 universities initiated a yearly conference on digital twin and smart manufacturing service, which is the first of its kind. The conference, which has been held four times, gathers world- renowned scholars to build a high-level international exchange platform and lead the innovation and development of science, technology and engineering in digital twins. The 5th event is scheduled for July 16-18, 2021, in Shanghai. In April 2021, we also launched an international, comprehensive journal called Digital Twin with Taylor & Francis, which will cover theoretical, technological and application innovations of digital twins.