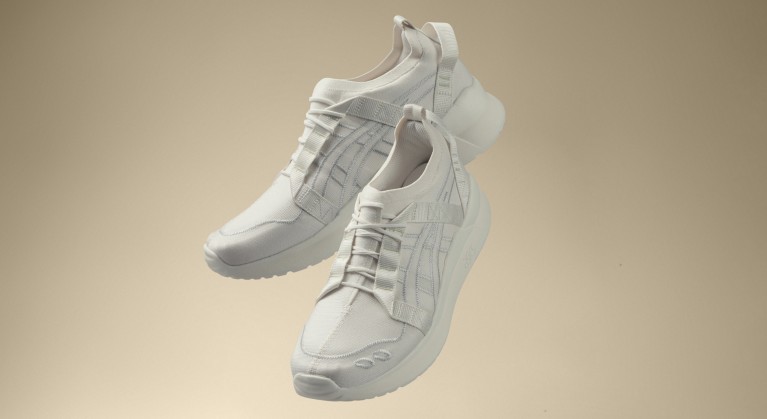
The product lifecycle of a pair of GEL-LYTE III CM 1.95 sneakers (pictured) emits just 1.95 kilograms of CO2-equivalent. This is less than one forth of the emissions generated by producing a typical pair of similar sneakers.Credit: ASICS
Most shoes come with an outsized carbon footprint. Estimates suggest the 20 billion shoes made each year may contribute to as much as 1.4% of global greenhouse gas emissions. As countries seek to limit the effects of climate change, shoe manufacturers must keep pace.
ASICS has now made a pair of shoes that may be the world’s lowest carbon sneakers on the market.* The Japanese firm reports the entire lifecycle of the streamlined mesh and foam GEL-LYTE III CM 1.95 sneaker emits just 1.95 kilograms of CO2-equivalent (CO2e) — a measurement of the total greenhouse gases emitted.This includes the greenhouse gases emitted to manufacture, transport, use and dispose of a pair.
In contrast, the overall carbon footprint of a typical pair of running shoes made of synthetic fuel-based materials is about 14 kg of CO2e, a collaboration between the Massachusetts Institute of Technology (MIT) in the United States and ASICS has found.1 And, the average ASICS sneaker creates about 8 kg of CO2e. That means the GEL-LYTE III CM 1.95 produces some 76% less CO2 emissions than the average shoe.
This reduction process will soon extend to more products, as part of a wider commitment by ASICS to reduce CO2 emissions across the company by 63% by 2030, based on its 2015 result. ASICS’s mission is “a sound mind, in a sound body for future generations through sports”, says Minako Yoshikawa, a senior general manager at the ASICS Sustainability Division, based in Kobe, Japan. And the eventual aim, she says, is to achieve net-zero emissions by 2050.
This target has meant that ASICS has been the first sporting goods company to have its target to reduce CO2 emissions approved by the international Science Based Targets Initiative, an organization set up by the United Nations and others that checks and validates corporate sustainability efforts.
Working with academia
It’s easy to claim low-carbon status for products, but it’s a much more complicated task to verify those claims, points out Yoshikawa. That’s especially true for shoes, which frequently rely on technical materials drawn from a diverse supply chain. Collaborative research conducted by MIT and ASICS found that a typical single running shoe could contain 65 discrete parts that require 360 processing steps for assembly.
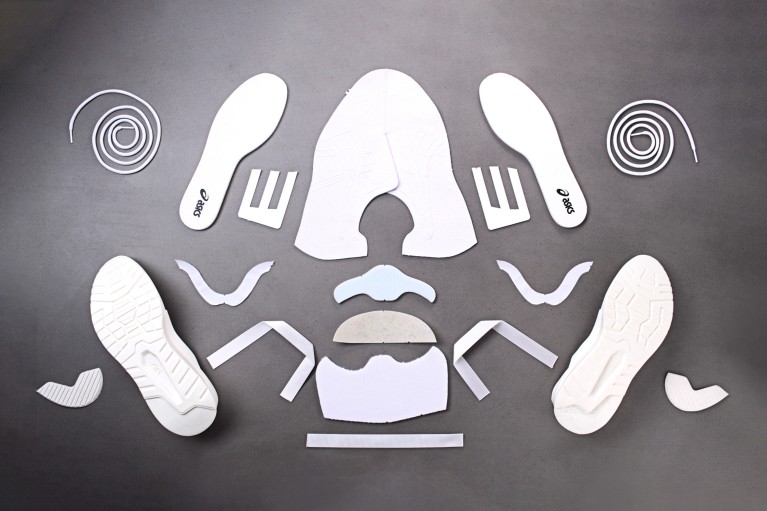
The GEL-LYTE III CM 1.95 has roughly 50% fewer parts compared to a conventional sneaker.Credit: ASICS
How shoes are made is pretty complex, explains Yoshikawa. More than 10 years ago, the ASICS team worked with MIT to conduct a comprehensive analysis of where, when, and how much CO₂ was released during the typical lifecycle of a pair of shoes and tried to figure out strategies to reduce the emissions.
The assessment, published in the Journal of Cleaner Production in 20131, broke down every aspect of the production. It reported, for example, how most of the processing steps involve cutting and stitching together the 53 parts in a shoe’s upper.
That all takes fuel and electricity, which helps to explain why the materials processing and manufacturing stages of the sneakers’ life cycle was found to typically generate the most CO2 emissions — about 29% and 68% of the total impact respectively.
“That research has helped us to really understand the emission details behind a shoe,” says Takao Arai, a sustainability specialist with ASICS. “Our experience, underpinned by academic work, have been key in helping find emissions reductions.”
Stepping on bottles
The bulk of the GEL-LYTE III CM 1.95 emissions savings is about the materials used and the way they are put together, explains Arai. The upper fabric is made from recycled plastic bottles, for example, while other components include mostly bio-based plastic foams produced partly from sugar cane.
Foam materials designed for durability are usually hard, which was not good for shoe cushioning. “So we applied several bio-based thermoplastic materials to improve softness and CO2 emissions, which helped us achieve new levels of sustainability without compromising on comfort and quality,” says Kenichi Harano, executive officer and senior general manager at the Institute of Sport Science at ASICS.
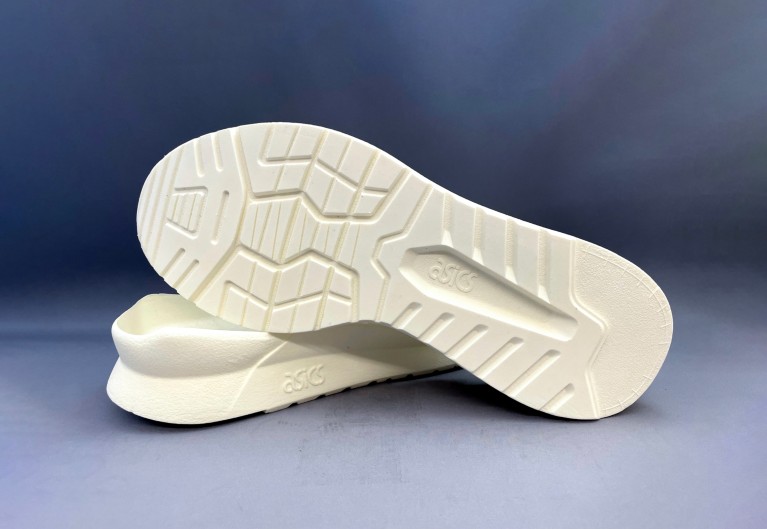
A functional thermoplastic material with soft properties was combined with a sugar-cane based foam for a comfortable, more sustainable sole.Credit: ASICS
Other design changes include a roughly 50% reduction in the overall number of parts required, as well as using a solution dyed upper textile and thread for the embroidered designs on the shoes. This way of colouring synthetic yarns is more energy efficient as it adds dye to a bulk polymer before filaments are drawn out, which reduces water use by a third and associated carbon emissions by 45%. In addition, the shape of the reinforcements on the upper shoe were re-designed to reduce material use.
Through these techniques, and others, the company reduced the CO2 emissions from its materials and manufacturing stages by almost 80% for the GEL-LYTE III CM 1.95.
Trimming CO2 emissions from the other stages was difficult, Arai says. “The challenge was the collaboration with suppliers. We couldn’t deliver without their support,” he says. “The success only came because we had great discussions on achieving this mission with them at every stage.”
Help from the company’s suppliers enabled a switch to biofuel to transport the finished products. While removing the wrapping paper from around and inside the shoes, and using recycled boxes, helped lower the CO2 emissions associated with packaging.
Global standards
Arai points out that the carbon-benchmarking process developed by MIT and ASICS is published and aligns with international standards. This allows the company, and its competitors, to repeat the CO2-reduction process with other shoe types, starting with a thorough and reliable assessment of life-cycle emissions.
“The objectivity of the calculation, and credible information and numbers are really important to consumers,” says Arai. “To guarantee such credibility and objectivity we thought that validation from a third party was necessary.”
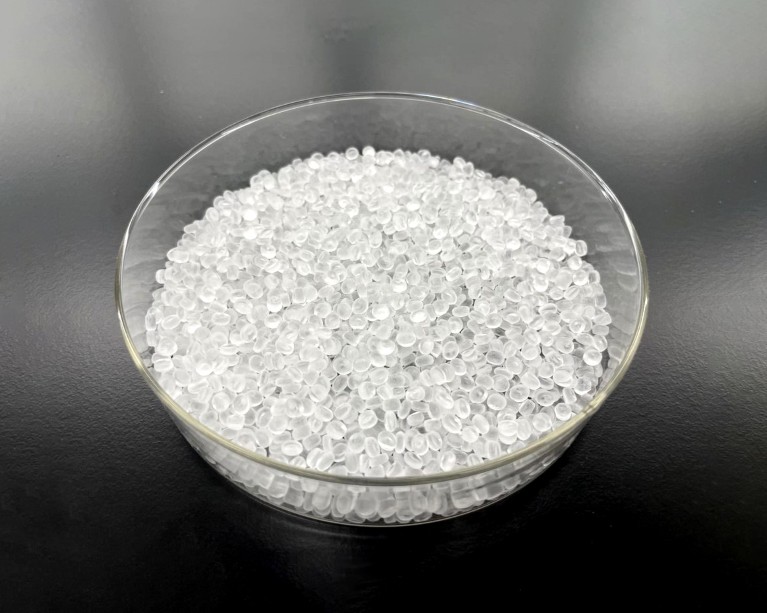
The midsole and sockliner of ASICS' innovative GEL-LYTE III CM 1.95 shoes are made using a foam produced partly from a sugar-cane based bioplastic.Credit: ASICS
ASICS has already published a breakdown of the carbon footprint of another of its popular running shoes, the GEL-KAYANO 30. “We’ll be expanding our effort to more shoes, including performance running shoes,” says Harano.
To achieve the 2050 net-zero goal, the company is also working to expand its use of renewable energy, Harano adds, as well as developing new low-carbon-footprint products using a protein based on spider silk, which could replace conventional plastics.
It has also pledged to adopt a circular approach to its operations, which means using less materials, reusing others and making longer-lasting products.
“I think our industry is pretty active at working on reducing the environmental impact,” says Yoshikawa. “Our purpose is to enable people to have a sound mind and sound body through sports. And that’s why we have committed to doing our part.”
*Based on available industry data for lifecycle CO2e emissions as of Sep 2023.
Find out more about the GEL-LYTE III CM 1.95 sneaker.