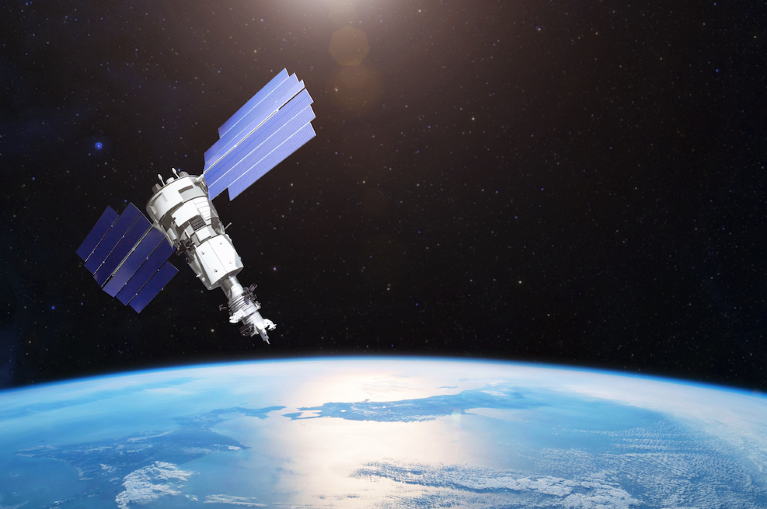
Whether observing astronomical objects in outer space or monitoring the Earth’s atmosphere, instruments on probes usually require cooling to cryogenic temperatures.© aappp/Shutterstock
Space-based probes are vital tools for enabling scientists to understand our planet and the wider Universe. For example, some satellites monitor the chemistry of the Earth’s atmosphere, while a growing swarm of space telescopes peer into the deepest recesses of the cosmos to explore supernova explosions, black holes and galaxy clusters.
All of these automated spacecraft, or probes, employ sensors to detect incredibly faint signals from their targets, including infrared light, gamma rays, X-rays and other frequencies of electromagnetic radiation. In most cases, these sensors work best when they are kept very cold, perhaps just a few degrees above absolute zero (0 kelvin or −273 °C).
In an infrared sensor, for example, any warmth would show up as thermal noise that would potentially swamp the elusive signals.
That’s where Sumitomo Heavy Industries Ltd (SHI), based in Ehime, Japan, comes in. “By using cryocoolers, we can reduce thermal noise in the sensors to boost the signal-to-noise ratio,” says Ken’ichi Kanao of SHI’s Engineering Department.
SHI began developing its cryogenic technologies in 1962 in Hiratsuka city, near Yokohama. It has created a range of low-temperature cryocooling systems that have played an invaluable role in space missions operated by the Japan Aerospace Exploration Agency (JAXA), the European Space Agency and NASA.
Today, SHI’s team of a dozen design engineers are continuing to push back the frontiers of cryocooling technology, developing new systems that can reliably deliver temperatures below 2 kelvin for many years.
The most common way of keeping instruments at cryogenic temperatures is to use a reservoir of liquid helium held in an insulated container known as a Dewar. Liquid helium has a temperature of 1 kelvin (−272 °C) in the vacuum conditions in space, and as it absorbs heat it boils to release helium gas. SHI have developed several compact Dewars that have low power consumptions thanks to their complex designs.
But once all the liquid helium has boiled away, the instrument it cooled will gradually warm up and eventually cease operating. Simply loading more liquid helium onto a space probe isn’t always an option, because carrying more mass into space requires bigger and more expensive rockets.
Keeping detectors cool
Since 1987, SHI has developed mechanical cryocoolers that do not depend on using a Dewar of liquid helium. Instead, these mechanical coolers are based on principles that have been known for centuries: gases warm up when compressed and cool down when they expand. By using repeating cycles of compression and expansion, these mechanical cryocoolers can carry heat away from sensors, and maintain temperatures as low as 1.7 kelvin for more than five years.
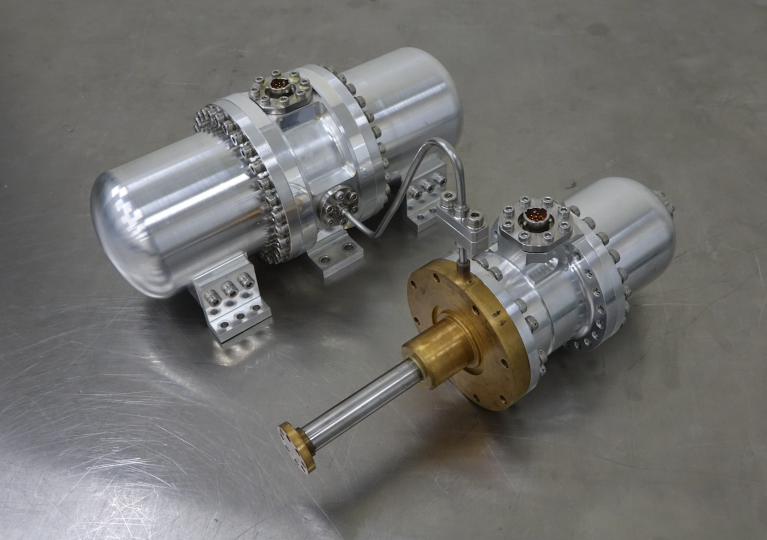
A single-stage Stirling cooler, which can used for cooling to 80 kelvin (−193 °C).© Sumitomo Heavy Industries
“There is a big advantage in lifetime compared with using liquid helium,” says Kanao.
Known as a Stirling cooler, one of these systems uses a mechanical pump to compress a gas such as helium, which then passes through a heat exchange system to cool it down. The gas is then expanded, which chills it below its original temperature. Repeating this cycle over and over enables an SHI Stirling cooler to maintain sensors at a temperature of 80 kelvin. In SHI’s labs, one of these units has operated for more than 18 years. A more advanced, two-stage Stirling cooler includes a second round of heat exchange and expansion, enabling the device to attain temperatures of 20 kelvin.
Improving cryocoolers
Over the years, SHI has made many design improvements to its cryocoolers. Perhaps the most important, says Kanao, is a spring that reduces friction between the piston and cylinder in the pump, improving its efficiency and prolonging its life. “This guarantees long lifetimes,” Kanao says. The gas used in the cryocoolers is also rigorously purified during manufacture, he adds, because trace contaminants such as carbon dioxide or water can form a solid ice between the piston and cylinder, increasing friction.
Another type of cryogenic cooler, known as a Joule–Thomson cooler, can reach even lower temperatures. This cooler also relies on compression and expansion cycles, but operates by forcing a gas through a valve. SHI can link these mechanical systems so that Stirling coolers act as a precooling stage for a Joule–Thomson cooler, ultimately lowering temperatures down to 4 kelvin.
These systems can thus keep a Dewar of liquid helium cold, slowing the inexorable boil off of helium gas. This hybrid approach has been used on two space probes, including the ill-fated Hitomi X-ray satellite that launched in 2016 to study processes such as how galaxy clusters evolve and how matter spirals into black holes.
Problems with Hitomi’s control system meant that its mission was short lived. But the cryogenics worked as expected, and a similar system has been installed on Hitomi’s successor, the X-Ray Imaging and Spectroscopy Mission (XRISM), which was launched in September 2023.
Hitting 1.7 kelvin
Back in the lab, SHI engineers have adapted their hybrid system so that it can reach temperatures of just 1.7 kelvin. The key difference is that the Joule–Thomson cooler in this system uses a lighter isotope of helium gas, known as helium-3. This has a higher vapour pressure than everyday helium-4, and a slightly lower boiling point. SHI’s 1.7 kelvin system can be used to absorb waste heat from a magnetic cryocooler that chills instruments to a mere 0.05 kelvin.
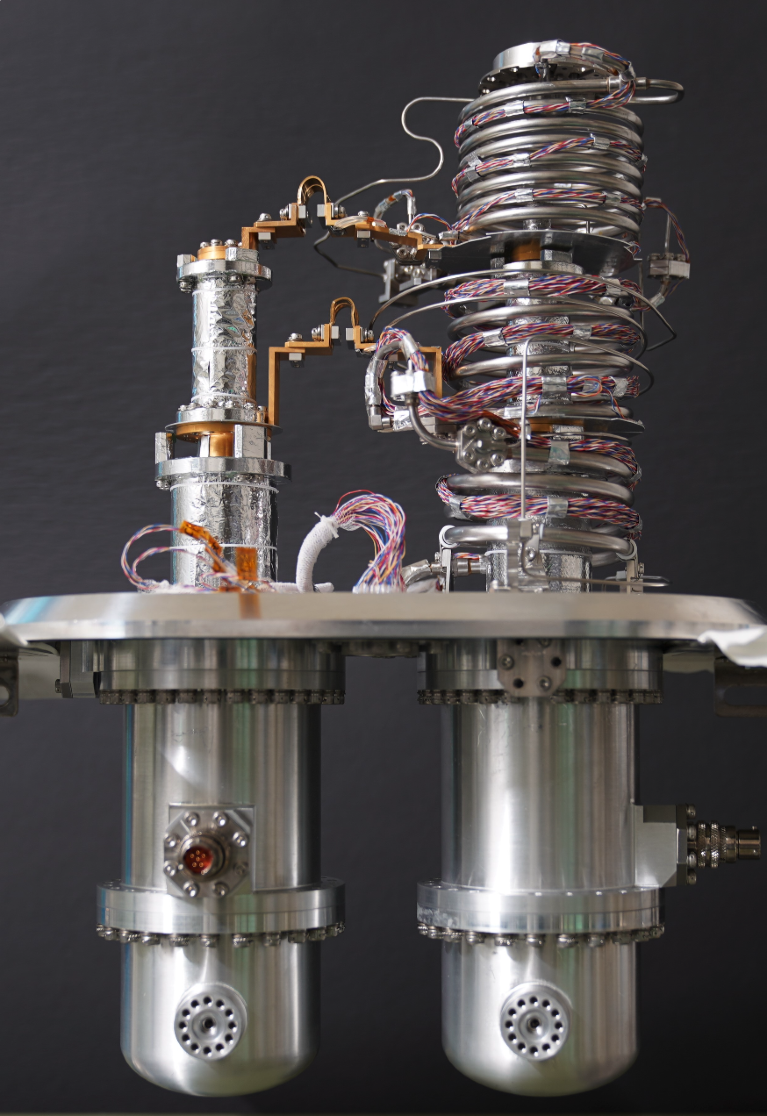
The Joule–Thomson cooler with precoolers used on the X-Ray Imaging and Spectroscopy Mission, or XRISM, which is shown here minus its compressors.© Sumitomo Heavy Industries
Development of the 1.7 kelvin system started back in the 1990s, and a working unit has been operating in the lab for more than five years. During this time, engineers have put the system through numerous tests to assess its performance and to ensure that it works in the vacuum conditions of space.
The 1.7 kelvin system is now ready to make its first flight into space aboard JAXA’s LiteBIRD mission, slated to launch around 2030. LiteBIRD aims to detect traces of the gravitational waves generated immediately after the Big Bang, by studying the characteristic fingerprints they left in the cosmic microwave background radiation that pervades the Universe.
Meanwhile, SHI’s engineers are making further design improvements to their mechanical cryocoolers. Their next frontier is not to reach lower temperatures, however — they are instead focused on building more-efficient units that can operate for even longer in space. They are also developing mechanical cryocoolers that deliver more cooling power, which could chill larger arrays of instruments.
Kanao says that SHI’s mechanical cooling systems will eventually replace Dewar technology altogether, potentially reducing the overall mass of cooling systems needed on future space probes. “We think that the next generation of technology will use only mechanical coolers, without liquid helium,” he says.